OCEAN CHALLENGER STRUCTURAL STEEL ROBOTIC WELDER
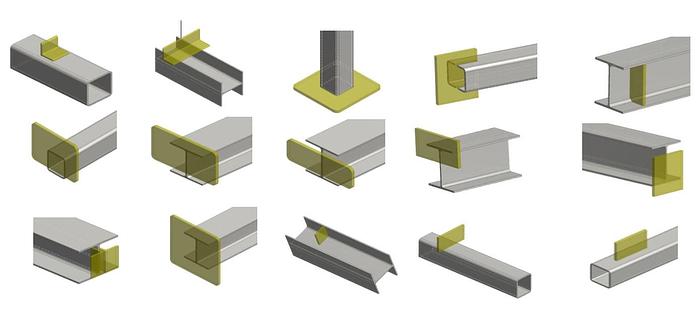
OCEAN CHALLENGER STRUCTURAL STEEL ROBOTIC WELDER
Description
The Ocean Challenger Robotic Welder is a fully automated structural steel welding robot that welds attachments to beams and columns that have been tacked in place by the fitter. AUTOMATED: The entire welding process is automated; the Ocean Challenger robotic welder only requires a fitter to tack the parts in place and position the beam or column into the production zone. The Ocean Challenger handles the mundane welding tasks by automatically welding the attachments to your beams and columns, allowing your experienced welders to work on more challenging projects. FLEXIBLE: The Ocean Challenger is designed for beams and columns up to 40” high, it is compatible with attachments such as angles, stiffeners, gussets, fin plates, base plates, end plates and other standard parts. EFFICIENT: The Ocean Challenger welding robot is designed to fabricate most steel assemblies and attachments for structural steel, typically able to weld 75% to 95% of all attachments. QUALITY: Robots are designed to work in harsh conditions for years with minimal maintenance ensuring consistent high-quality and repeatable results. EASY-TO-USE: Compatible with Tekla & SDS2. Simply export the CAD model to the Ocean Challenger, run the simulation, select the exported simulation file using the Ocean Challenger’s user-friendly interface, load the part and start production! SAFETY: The Ocean Challenger comes with a laser light curtain that automatically stops the machine when the perimeter is crossed, ensuring operator safety. Meets American ANSI/RIA R15.06-2012, and Canadian CSA Z434-14 safety standards. SUPPORT: Any issues are handled directly by the experts at AGT. Most problems can be addressed quickly using remote web support with qualified technicians logging in remotely and accessing the machine interface & webcam so they can see what you see. For more complex issues a field technician can be dispatched to ensure you are up and running quickly.
Specifications
Manufacturer | Ocean Machinery |
Condition | New |
Robot | Fanuc Arc Mate 120i |
Welding equipment | Lincoln Electric R450 Power Source Wire Feeder Welding Torch Collision Detect Torch Cleaning Station (reamer) |
Typical welding speed – fillet welds (2f) | 20 in/min for 3/16’’ weld – (500mm/min for 5mm weld) 15 in/min for 1/4’’ weld – (380mm/min for 6.5mm weld) 10 in/min for 5/16″ weld – (250mm/min for 8mm weld) |
Beam size (effective welding zone) | Section – Minimum 6″ / Maximum 40″ Length – Minimum 4′ / Maximum 50′ |
Gap tolerances | Maximum 1mm – No Gap Detection |
Joint detection | Laser Touch Sensing |
Process and position | MCAW – Spray and Pulse Transfer – Horizontal (2F) or GMAW – Spray and pulse transfer – Horizontal (2F) |
Wire | MCAW: Hobart Fabcor Edge 0.045″ diameter (1.2mm) or GMAW: Lincoln Electric SuperArc L-59 0.045’’ diameter (1.2mm) |
Wire classification | MCAW: AWS A5.18, A5.18M: E70C-6M H4 / CSA W48-06: E491C-6MJ-H4 GMAW: AWS A5.18/A5.18M: ER70S-6 / CSA W48-06: ER49S-6 |
Shielding gas | 85% Argon – 15% CO2 mix |
Surface finish | All parts and beam must be clean & dry with low scale level |
Electrical | 480V 3ph 60Hz 50 kVA and 120V 1ph 60Hz 15A |
Pneumatic | 100 psi @ 20 CFM Clean Air 0.005MM Dry 99.9%, Unlubricated, 1/2″ NPT |
Ethernet speed | Upload / Download speed > 10Mbs |
Footprint w/console & safety barrier | 68′ x 15′ x 12’H |
Weight | 20,000 lbs. |